- Partilhar artigo
- ...
Só em 2018, a Novares Portugal, instalada em Leiria, equipou mais de 6,7 milhões de automóveis que circulam um pouco por todo o mundo. Falamos de marcas de topo de gama, mas também de gamas mais baixas, desde a Audi, BMW, Bentley, Toyota à Fiat, Alfa Romeo, Volkswagen, que utilizam peças em plástico produzidas nesta indústria.
A unidade portuguesa da multinacional Novares, grupo que nasceu da fusão, em 2017, dos grupos Macplast e Key Plastics, ambos fornecedores de soluções integradas de peças em plástico para a indústria automóvel, detém o centro de competência da marca para as áreas de painéis frontais e os painéis de instrumentos dos automóveis. O grupo, que faturou 1,4 mil milhões de euros em 2018, tem presença direta em 12 países com 47 fábricas, e emprega 12 mil pessoas, tem oito centros de competência no mundo, estando um deles em Portugal. É daqui que partem muitas das inovações que são esenvolvidas pela área de Investigação e Desenvolvimento (I&D), que ocupa perto de 30 engenheiros multidisciplinares.
É com os olhos postos no futuro que a filial nacional, com cerca de 600 pessoas e que consolida ainda a fábrica de Vendas Novas, está a investir nas instalações da Barosa, em Leiria. Especializada na produção de painéis com botões, tudo aponta para que estes deixem, gradualmente, de ser utilizados. "Os produtos que a Novares ainda faz para os fornecedores de primeira linha dos construtores automóveis estão a desaparecer. Agora, a grande tendência, sobretudo nos veículos topo de gama, são os painéis ‘seamless’ [lisos], em grandes blocos integrados e totalmente digitais", explica Gilberto Landim, diretor da unidade fabril de Leiria.
Tendo isto em conta, esta transição é fundamental para a sobrevivência do negócio. A unidade portuguesa iniciou, para isso, um investimento de dois milhões de euros para uma nova linha de produção equipada com a tecnologia IML ("In-Mold Labelling"), que permitirá imprimir decorações, desenhos e carateres funcionais, diretamente numa folha plástica, que serão depois conformados em geometrias tridimensionais e sobremoldados no componente plástico. Desta forma vai ser possível criar versões mais modernas dos frontais e painéis com tecnologia "touch" (tátil), ou seja, sem botões e sem ligações entre os componentes plásticos, com a integração de ecrãs digitais. "Porém, os produtos tradicionais não irão desaparecer totalmente porque há clientes que os preferem", explica Gilberto Landim.
Inovar para crescer
A inovação é um dos principais eixos de crescimento da multinacional. José Vasco, diretor de engenharia de manufatura, revela que a Novares vai investir cerca de 50 milhões de euros nos próximos cinco anos em I&D, o que corresponde a cerca de 5,4% do volume de negócios anual. Explica ainda que existem três pilares fundamentais para a inovação: o primeiro é via cliente, ou seja, através da sua encomenda; o segundo tem a ver com o que é desenvolvido nos laboratórios de demonstração de tecnologias, e é neste pilar que se inclui o projeto Novacar 2, que estima o que será um carro no futuro e apresenta as soluções que poderá disponibilizar aos clientes. Este modelo de demonstração de inovação permite promover a marca e facilita a sua entrada nos grandes grupos automóveis. O terceiro pilar de inovação passa pela aquisição de start-ups, para ganhar agilidade e contaminar toda a estrutura com as suas tecnologias e ideias.
50
65
6,7
Os principais clientes da Novares Portugal são a Bosh, a Continental, a Visteon, a Faurecia, fornecedores de componentes que integram estas peças nos seus produtos e os revendem aos construtores automóveis. Canaliza cerca de 65% das suas vendas, que atingiram os 50 milhões em 2018, para a República Checa (37%) - onde está instalada a fábrica da Continental -, a Alemanha, a Espanha, a Hungria e a Ucrânia, com percentagens mais baixas. Os 35% de produção restante fica em Portugal nas fábricas da Visteon e da Bosh. Uma vez que equipam modelos de alta gama, como o Audi A6, A7 e S8, os padrões de exigência são elevados, pelo que o controlo de qualidade é um aspeto relevante para o negócio. Os equipamentos para os testes e medições são desenvolvidos no centro de competência e são fornecidos a outras empresas do grupo, explica Gilberto Landim.
Perguntas a Gilberto Landim
Diretor de produção da Novares
Investir 3 a 4 milhões anualmente
Destinado a melhorias contínuas na fábrica, como o redesenho de "layout" ou a substituição de equipamentos, a empresa investe continuamente no seu negócio para se manter atualizada.
Como decorreu a vossa atividade em 2018, e qual o volume de negócios registado?
Em 2018 houve uma quebra geral nas encomendas da indústria automóvel. Essa quebra é devida ao adiamento na decisão de compra de viaturas. Contudo registamos uma faturação de 50 milhões de euros, o que foi apenas um ligeiro crescimento face ao que estimávamos inicialmente. Esperamos uma recuperação do ritmo de crescimento já em 2020.
Essa recuperação é baseada em que fatores? Na nova unidade de IML?
A nova linha de IML ainda não trará grande impacto no volume negócios do próximo ano. Temos é outros produtos que entraram agora em produção que vão trazer mais resultados, que são os painéis de instrumentos digitais com destino ao grupo Volkswagen, através das encomendas da Visteon e da Continental. A Volkswagen fez "dual sourcing", ou seja, entregou parte da encomenda à Visteon e parte à Continental, e as duas vieram produzir à Novares, em Leiria.
O investimento inicial na unidade de IML foi de dois milhões. Quanto estimam investir no total?
Atualmente o investimento já está em 2,8 milhões de euros, mas é difícil prever o valor total porque tudo depende da procura que tivermos. A realização de mais investimentos no futuro vai depender das necessidades específicas dos nossos clientes.
Para além desse investimento que outros estão a realizar? Quanto investem anualmente?
Os nossos investimentos anuais rondam sempre os três a quatro milhões em melhoria contínua na fábrica, como sejam as mudanças de "layout", de fluxos, e a substituição de máquinas e equipamentos.
Qual o vosso objetivo em termos estratégicos para o futuro?
Para já o grande objetivo passa por desenvolver a nova linha de IML que é o futuro desta indústria. E estamos ainda a discutir a possibilidade de aumentar a capacidade dos equipamentos, porque neste momento estamos a receber pedidos de clientes para peças muito grandes para as quais não temos ainda capacidade instalada. Ou seja, temos máquinas de injeção com tonelagens pequenas e o mercado está a pedir peças que necessitam de máquinas com tonelagens maiores.
A unidade portuguesa da multinacional Novares, grupo que nasceu da fusão, em 2017, dos grupos Macplast e Key Plastics, ambos fornecedores de soluções integradas de peças em plástico para a indústria automóvel, detém o centro de competência da marca para as áreas de painéis frontais e os painéis de instrumentos dos automóveis. O grupo, que faturou 1,4 mil milhões de euros em 2018, tem presença direta em 12 países com 47 fábricas, e emprega 12 mil pessoas, tem oito centros de competência no mundo, estando um deles em Portugal. É daqui que partem muitas das inovações que são esenvolvidas pela área de Investigação e Desenvolvimento (I&D), que ocupa perto de 30 engenheiros multidisciplinares.
É com os olhos postos no futuro que a filial nacional, com cerca de 600 pessoas e que consolida ainda a fábrica de Vendas Novas, está a investir nas instalações da Barosa, em Leiria. Especializada na produção de painéis com botões, tudo aponta para que estes deixem, gradualmente, de ser utilizados. "Os produtos que a Novares ainda faz para os fornecedores de primeira linha dos construtores automóveis estão a desaparecer. Agora, a grande tendência, sobretudo nos veículos topo de gama, são os painéis ‘seamless’ [lisos], em grandes blocos integrados e totalmente digitais", explica Gilberto Landim, diretor da unidade fabril de Leiria.
Tendo isto em conta, esta transição é fundamental para a sobrevivência do negócio. A unidade portuguesa iniciou, para isso, um investimento de dois milhões de euros para uma nova linha de produção equipada com a tecnologia IML ("In-Mold Labelling"), que permitirá imprimir decorações, desenhos e carateres funcionais, diretamente numa folha plástica, que serão depois conformados em geometrias tridimensionais e sobremoldados no componente plástico. Desta forma vai ser possível criar versões mais modernas dos frontais e painéis com tecnologia "touch" (tátil), ou seja, sem botões e sem ligações entre os componentes plásticos, com a integração de ecrãs digitais. "Porém, os produtos tradicionais não irão desaparecer totalmente porque há clientes que os preferem", explica Gilberto Landim.
Inovar para crescer
A inovação é um dos principais eixos de crescimento da multinacional. José Vasco, diretor de engenharia de manufatura, revela que a Novares vai investir cerca de 50 milhões de euros nos próximos cinco anos em I&D, o que corresponde a cerca de 5,4% do volume de negócios anual. Explica ainda que existem três pilares fundamentais para a inovação: o primeiro é via cliente, ou seja, através da sua encomenda; o segundo tem a ver com o que é desenvolvido nos laboratórios de demonstração de tecnologias, e é neste pilar que se inclui o projeto Novacar 2, que estima o que será um carro no futuro e apresenta as soluções que poderá disponibilizar aos clientes. Este modelo de demonstração de inovação permite promover a marca e facilita a sua entrada nos grandes grupos automóveis. O terceiro pilar de inovação passa pela aquisição de start-ups, para ganhar agilidade e contaminar toda a estrutura com as suas tecnologias e ideias.
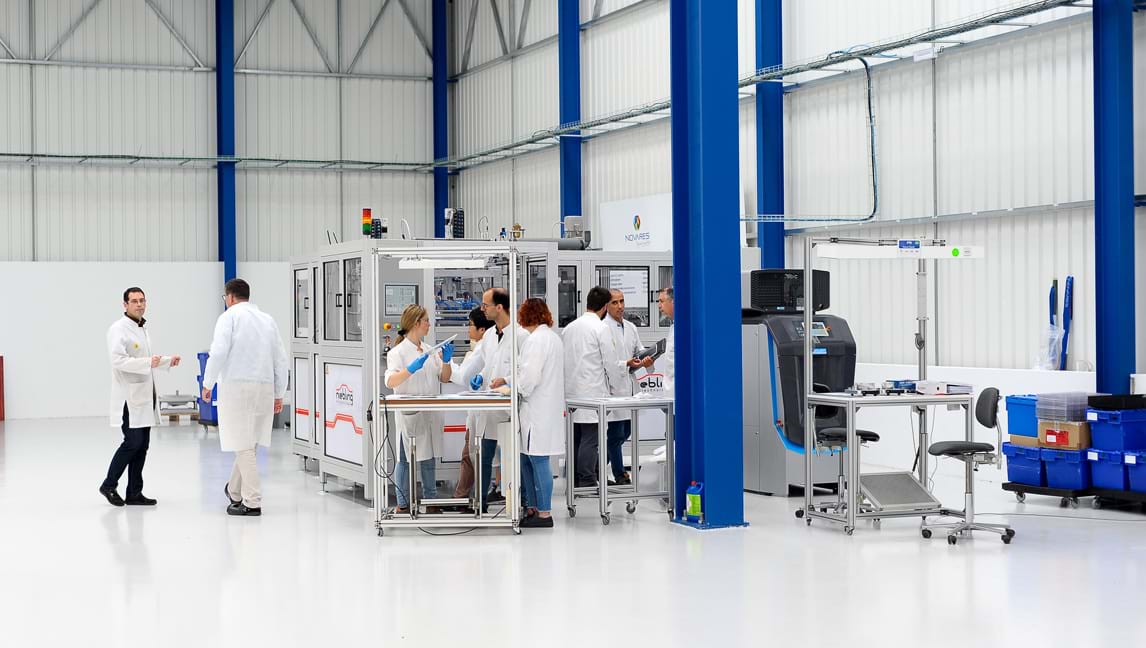
50
Faturação
As vendas da empresa atingiram os 50 milhões de euros em 2018.
65
Exportações
O peso das exportações atinge os 65% do volume de vendas anual.
6,7
Veículos
Em 2018, as peças da Novares de Leiria integraram 6,7 milhões de carros.
Os principais clientes da Novares Portugal são a Bosh, a Continental, a Visteon, a Faurecia, fornecedores de componentes que integram estas peças nos seus produtos e os revendem aos construtores automóveis. Canaliza cerca de 65% das suas vendas, que atingiram os 50 milhões em 2018, para a República Checa (37%) - onde está instalada a fábrica da Continental -, a Alemanha, a Espanha, a Hungria e a Ucrânia, com percentagens mais baixas. Os 35% de produção restante fica em Portugal nas fábricas da Visteon e da Bosh. Uma vez que equipam modelos de alta gama, como o Audi A6, A7 e S8, os padrões de exigência são elevados, pelo que o controlo de qualidade é um aspeto relevante para o negócio. Os equipamentos para os testes e medições são desenvolvidos no centro de competência e são fornecidos a outras empresas do grupo, explica Gilberto Landim.
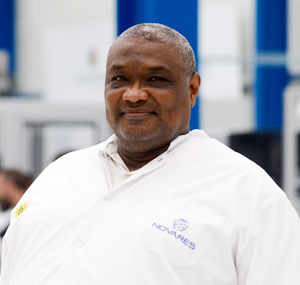
Diretor de produção da Novares
Investir 3 a 4 milhões anualmente
Destinado a melhorias contínuas na fábrica, como o redesenho de "layout" ou a substituição de equipamentos, a empresa investe continuamente no seu negócio para se manter atualizada.
Como decorreu a vossa atividade em 2018, e qual o volume de negócios registado?
Em 2018 houve uma quebra geral nas encomendas da indústria automóvel. Essa quebra é devida ao adiamento na decisão de compra de viaturas. Contudo registamos uma faturação de 50 milhões de euros, o que foi apenas um ligeiro crescimento face ao que estimávamos inicialmente. Esperamos uma recuperação do ritmo de crescimento já em 2020.
A nova linha de IML ainda não terá impacto nas receitas de 2020. Gilberto landim
Diretor de produção da Novares em Leiria
Diretor de produção da Novares em Leiria
Essa recuperação é baseada em que fatores? Na nova unidade de IML?
A nova linha de IML ainda não trará grande impacto no volume negócios do próximo ano. Temos é outros produtos que entraram agora em produção que vão trazer mais resultados, que são os painéis de instrumentos digitais com destino ao grupo Volkswagen, através das encomendas da Visteon e da Continental. A Volkswagen fez "dual sourcing", ou seja, entregou parte da encomenda à Visteon e parte à Continental, e as duas vieram produzir à Novares, em Leiria.
O investimento inicial na unidade de IML foi de dois milhões. Quanto estimam investir no total?
Atualmente o investimento já está em 2,8 milhões de euros, mas é difícil prever o valor total porque tudo depende da procura que tivermos. A realização de mais investimentos no futuro vai depender das necessidades específicas dos nossos clientes.
Para além desse investimento que outros estão a realizar? Quanto investem anualmente?
Os nossos investimentos anuais rondam sempre os três a quatro milhões em melhoria contínua na fábrica, como sejam as mudanças de "layout", de fluxos, e a substituição de máquinas e equipamentos.
Qual o vosso objetivo em termos estratégicos para o futuro?
Para já o grande objetivo passa por desenvolver a nova linha de IML que é o futuro desta indústria. E estamos ainda a discutir a possibilidade de aumentar a capacidade dos equipamentos, porque neste momento estamos a receber pedidos de clientes para peças muito grandes para as quais não temos ainda capacidade instalada. Ou seja, temos máquinas de injeção com tonelagens pequenas e o mercado está a pedir peças que necessitam de máquinas com tonelagens maiores.